It started with a simple
thought. I saw some off road bikers with GoPro Hero cameras mounted on
their helmets, and wondered if this idea would make a good lamp. My
original idea was to duplicate the camera as an aluminium, heat sink
finned box with the GoPro window set in the front. Some experimentation
revealed that the window was far too small to cover any effective
reflector combination. However, playing around with the idea convinced
me that is was a very good one in that a box with its flat surfaces will
mount just about anything. So if driver boards become discontinued, I
can use a different one, whatever.
There is a
huge advantage with using GoPro mounting as the lamp can be mounted on
virtually anything with the wide range of different mountings available.
GoPro is the future.
Obviously a round glass
similar to my other lamps would be easily obtainable and could be direct
bonded to the front of the lamp same as a car windscreen. This is
already used in the Dragon. Obviously a surround would be needed to
protect the glass. Another advantage would be increased water
resistance. The Chinese die cast headset shells used in the Lynx lamp
are only rated to IP 67 which is 1 metre submersion for 30 minutes. I
have had lamps exceed this in very adverse conditions, such as a
waterfall that strong that the wearer could not even stand under it.
The Scorpion
is IP68 5 metres submersion, but obviously with a time limit due to risk
of water getting in from the cable plugs by travelling up inside the
cable sheathing.
I was also keen to put into
practice an idea I had in my head for some time. That of using a 12 volt
DC input to drive 3 emitters wired in series whereby two are placed
behind spot reflectors with the third as a bare emitter. This giving 2/3
of the power to the beams, 1/3 to the floodlight. I found that this is
the ideal combination, but my big bat cookers, by virtue of their size
and power, needed 3 to 3 beams to floods. The idea also occurred that
using a double throw switch I could have two groups of three each with a
totally independent circuit, as high range of settings and a low range
of settings. This was the original concept, the Scorpion X_12.
The problem
with 12 volt lighting is that it requires 3 series battery cells, so its
multiples of 3. 3 is OK on a helmet pack, but 6 gets big and heavy.
However recent advantages in LiIon battery technology by people such as
Sanyo Panasonic and Tesla have produced very high capacity high
discharge cells. So now a 3 cell helmet pack weighing in at 280
grams is good for 3.5 ampere hours at its nominal voltage of 11.2 volts.
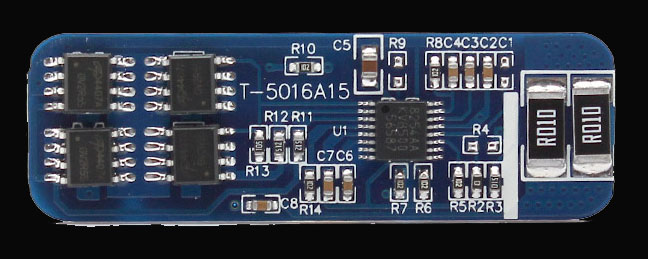
Left is the
MOSFET controlled battery management PCB that prevents overcharge, over
discharge, and short circuit. Typical of the high quality third party
components.
I also considered the finish.
I have a lamp returned for repair that looked as though it had been
dragged behind a Land Rover. A brightly polished and anodised lamp looks
nice when new but after some hard use looks a mess. Unfinished aluminium
will look the same in 12 months as when it was purchased.
Internally,
the lamp uses existing tried and tested components.
The low
range beams on the X_12 are by Cree XP-G 2 emitters which will throw a
decent beam from small reflectors and in my o pinion
give best brightness at low currents.
They
are mounted behind excellent, but expensive, Ledil optics and are really
very good for their size.
These have
previously been used as the pilots in some of my big bat cookers.
Having assembled a prototype
and tested it it now occurred that it would be a good idea to offer a
second model similar to my ever popular Lynx X2000. But offering
improved water resistance and a shorter heat track between the floods
and ambient.
Thus was
born the second in the series, the Scorpion X_8. Exactly the same inside
as the Lynx X2000 but with double the supplementary floodlight which
comes on with the beam. Now at 100 mA it matches the standard beam mode
on the 'magic' 2 to 1 ratio like the X_12. This is the lamp for those
who prefer a lamp with independent floodlights. The Lynx X2000 is a
cheaper alternative but the Scorpion has the GoPro and IP 68 benefit and
also better heat dissipation from the floodlights as the heat has only
10mm to travel to ambient.
The final
model is TGX, This will be produced in various LED configurations
but as a lamp permanently connected to the battery case to prevent water
ingress by travelling up inside the cable.
I have now
been producing lamps for 10 years and have stayed with my established
principle of wiring multiple LEDs in series matched to the input
voltage. This is a sure formular for combining very high outputs with
maximum efficiency. I have always used off the shelf components, often modified, in
order to keep the price down. The lamp body is manufactured in
Scunthorpe, the switches are from Germany, cable Italy, the only
complete outsourced component is the circular glass protector which is
from Lazermaster in Cornwall. I have a small toolroom in an outbuilding
where a lot of machining or remachining is done myself, my electronics
lab is in the house.
The
lamp is intrinsically reliable by virtue of its design and very easy to
replace any individual component if the need arises. Both the X_8 and
X_12 have two totally independent electronic circuits plus a linear
backup built into the beams. The multiple series wired LED configuration
of the X_8 and X_12 provide the most powerful commercial practical head
lighting obtainable. I use copper which has double the thermal
conductivity of aluminium for the LED mounts.
The result
is a very competitively priced lamp that considerably outperforms lamps
costing more than double the price.
|